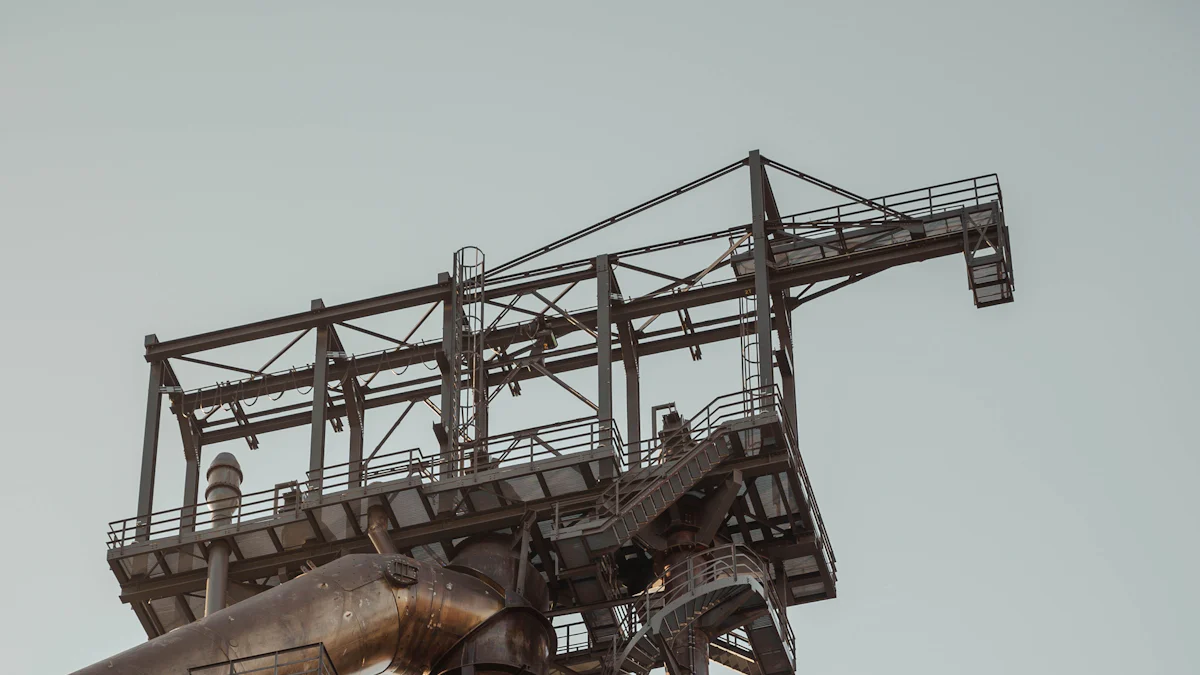
Durable and efficient jaw crusher parts play a vital role in heavy-duty applications. You rely on components like jaw plates, toggle plates, bearings, and pitman arms to handle tough materials with precision. These parts ensure your equipment operates smoothly, minimizing downtime and maximizing productivity. Selecting high-quality parts not only boosts performance but also reduces long-term costs. By investing in reliable components, you enhance the lifespan of your crusher and maintain consistent results in demanding environments.
Key Takeaways
- Invest in high-quality jaw crusher parts to enhance performance and reduce long-term costs.
- Choose the right type of jaw plates based on the material being crushed to ensure efficient operation and minimize wear.
- Regularly inspect and replace toggle plates to maintain stability and protect your equipment from damage.
- Select durable materials like high-manganese steel for jaw plates and bearings to withstand heavy loads and extend lifespan.
- Prioritize wear-resistant coatings to reduce maintenance needs and improve the longevity of your jaw crusher parts.
- Ensure compatibility of parts with your specific crusher model to prevent operational inefficiencies and potential damage.
- Consider customized parts for unique applications to enhance performance in challenging conditions.
Jaw Crusher Parts Overview
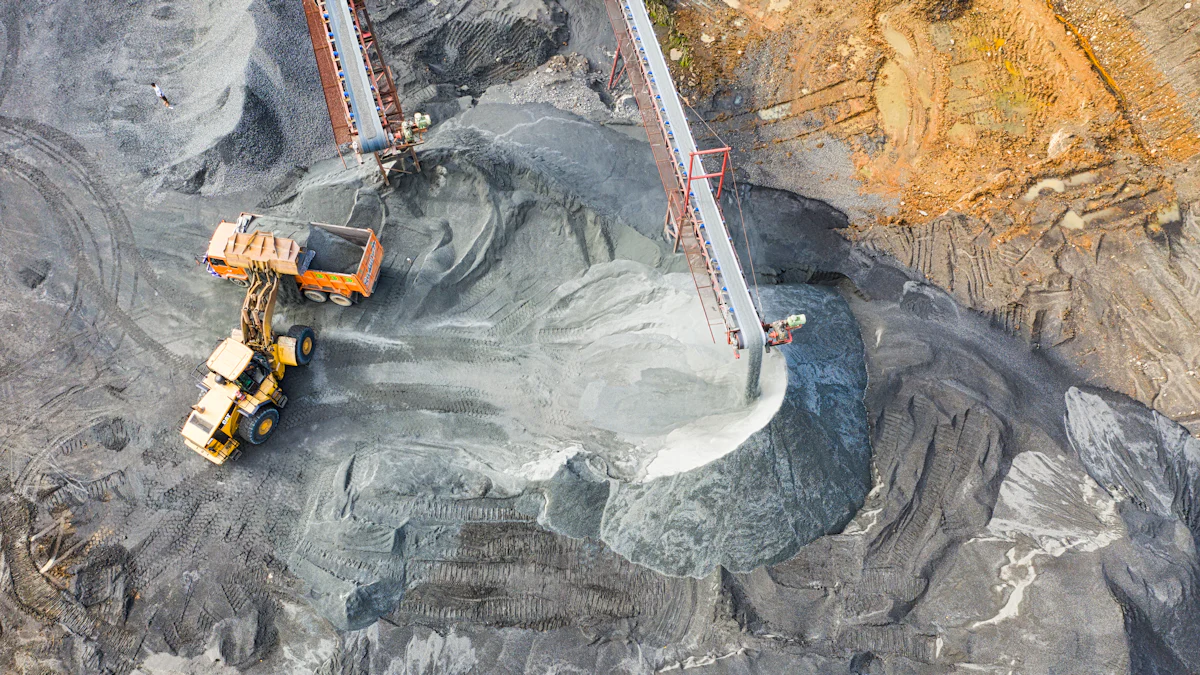
Jaw Plates
Types of jaw plates and their specific applications.
Jaw plates are the primary components that come into direct contact with the material being crushed. These plates are available in various types, each designed for specific applications. Flat jaw plates work well for general crushing tasks, while corrugated jaw plates are ideal for handling abrasive materials. Ribbed jaw plates provide enhanced grip, making them suitable for crushing hard rocks or ores. Selecting the right type of jaw plate ensures efficient crushing and reduces wear on the equipment.
Importance of jaw plates in crushing operations.
Jaw plates play a critical role in the crushing process. They exert immense pressure on the material, breaking it down into smaller pieces. High-quality jaw plates improve crushing efficiency and ensure consistent output. Poorly designed or worn-out plates can lead to uneven crushing, increased energy consumption, and frequent maintenance. By choosing durable jaw plates, you enhance the performance of your jaw crusher and minimize operational disruptions.
Toggle Plates
Role of toggle plates in maintaining crusher stability.
Toggle plates act as a safety mechanism and provide structural stability to the jaw crusher. These plates transfer force from the pitman to the moving jaw, enabling the crushing action. In case of excessive pressure or uncrushable material, the toggle plate breaks to prevent damage to other components. This feature ensures the longevity of your equipment and protects it during heavy-duty operations.
Key considerations for toggle plate material and design.
The material and design of toggle plates significantly impact their performance. High-manganese steel is a popular choice due to its strength and resistance to wear. The thickness and shape of the toggle plate should match the crusher’s specifications to ensure proper functionality. Regular inspection and timely replacement of toggle plates help maintain the stability and efficiency of your jaw crusher.
Bearings and Pitman Arms
Function of bearings in ensuring smooth operation.
Bearings are essential for the smooth operation of jaw crushers. They reduce friction between moving parts, allowing the machine to function efficiently. High-quality bearings withstand heavy loads and high temperatures, ensuring reliable performance in demanding conditions. Proper lubrication and regular maintenance of bearings prevent premature wear and extend their lifespan.
Importance of pitman arms in transferring motion and force.
Pitman arms serve as a crucial link between the eccentric shaft and the moving jaw. They transfer motion and force, enabling the crushing action. A robust pitman arm ensures consistent performance and minimizes stress on other components. Choosing a well-designed pitman arm made from durable materials enhances the overall efficiency of your jaw crusher.
Key Features of High-Quality Jaw Crusher Parts
Material Durability
Common materials used in jaw crusher parts and their benefits.
The durability of jaw crusher parts depends heavily on the materials used in their construction. Manufacturers often rely on high-manganese steel, alloy steel, and chromium steel for their exceptional strength and resistance to wear. High-manganese steel provides excellent toughness, making it ideal for parts like jaw plates that endure constant impact. Alloy steel offers a balance of strength and flexibility, ensuring components like toggle plates can handle stress without breaking. Chromium steel, known for its hardness, enhances the lifespan of parts exposed to abrasive materials. By selecting parts made from these materials, you ensure reliable performance in demanding environments.
How material durability impacts performance in heavy-duty applications.
Durable materials directly influence the efficiency and longevity of your jaw crusher. High-quality materials withstand the intense pressure and friction involved in crushing operations. This reduces the risk of part failure, ensuring consistent performance even under heavy loads. Durable components also minimize downtime caused by frequent replacements, saving you time and operational costs. When you invest in durable jaw crusher parts, you enhance the machine’s ability to handle tough jobs with ease.
Wear Resistance
Importance of wear-resistant coatings and treatments.
Wear resistance plays a critical role in extending the lifespan of jaw crusher parts. Coatings and treatments, such as heat treatment or carbide overlays, enhance the surface hardness of components. These processes reduce the rate of wear caused by constant contact with abrasive materials. For example, jaw plates with wear-resistant coatings maintain their structural integrity longer, ensuring consistent crushing performance. By prioritizing wear resistance, you reduce maintenance needs and improve the overall efficiency of your equipment.
How wear resistance reduces maintenance and extends part lifespan.
Wear-resistant parts require less frequent replacement, which lowers maintenance costs and minimizes downtime. Components like bearings and pitman arms benefit significantly from enhanced wear resistance, as they endure continuous motion and pressure. Improved wear resistance ensures these parts maintain their functionality over extended periods, even in harsh conditions. By choosing parts with superior wear resistance, you maximize the productivity of your jaw crusher while reducing long-term expenses.
Maintenance and Longevity
Features that simplify maintenance and improve part longevity.
High-quality jaw crusher parts often include features designed to simplify maintenance. For instance, modular designs allow for quick and easy replacement of worn components. Self-lubricating bearings reduce the need for frequent lubrication, saving you time and effort. Additionally, parts with clear wear indicators help you identify when replacements are necessary, preventing unexpected breakdowns. These features not only streamline maintenance but also contribute to the overall longevity of your equipment.
Examples of durable and long-lasting jaw crusher parts.
Several examples highlight the durability of well-designed jaw crusher parts. Jaw plates made from high-manganese steel resist cracking and deformation, even under extreme pressure. Toggle plates crafted from alloy steel provide reliable performance without frequent replacements. Bearings with advanced sealing systems prevent contamination, ensuring smooth operation over time. By incorporating these durable components into your crusher, you achieve consistent results and extend the machine’s operational life.
Top Brands and Manufacturers of Jaw Crusher Parts
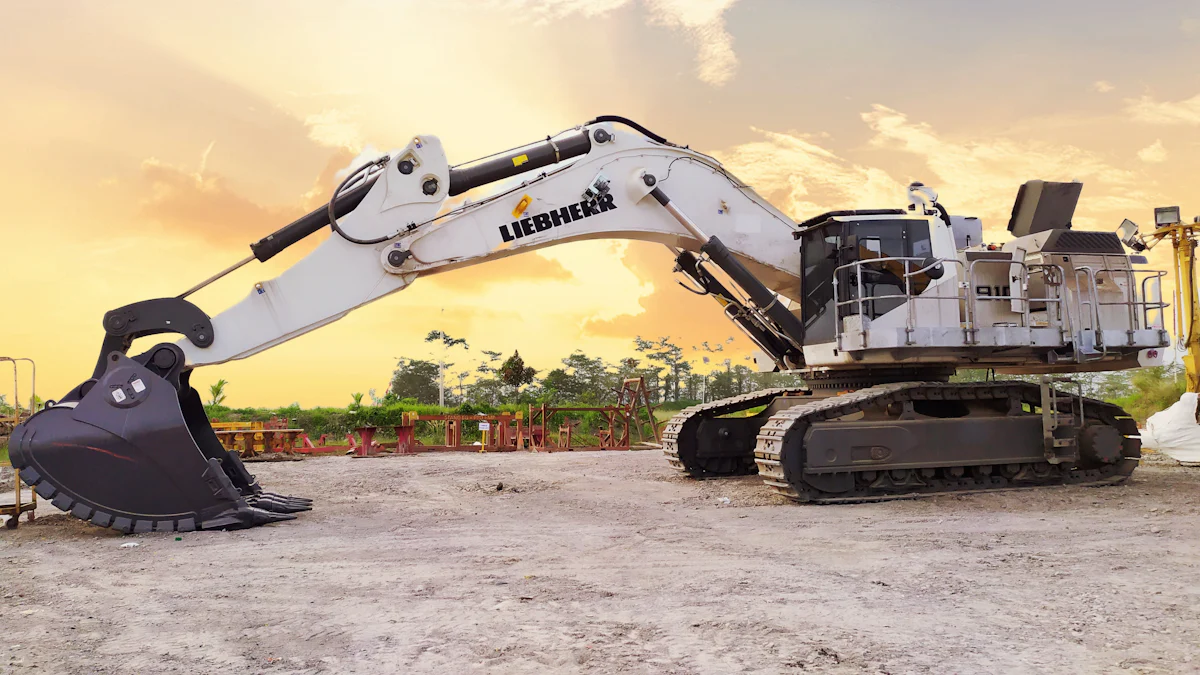
Leading Brands
Overview of top manufacturers in the jaw crusher industry.
When selecting jaw crusher parts, you should consider manufacturers known for their expertise and reliability. Some of the top names in the industry include Metso, Sandvik, and Terex. These companies have built strong reputations by consistently delivering high-quality components designed for heavy-duty applications. Their products undergo rigorous testing to ensure they meet the demands of challenging environments. By choosing parts from these trusted brands, you gain access to durable and efficient solutions that enhance your crusher’s performance.
Metso stands out for its innovative designs and commitment to sustainability. Sandvik focuses on precision engineering and advanced materials to create parts that last longer. Terex emphasizes versatility, offering a wide range of components compatible with various crusher models. Each of these manufacturers has a proven track record of producing reliable parts that help you achieve consistent results in your operations.
Key innovations and technologies offered by these brands.
Top manufacturers continuously invest in research and development to improve their products. Metso, for example, integrates wear-resistant alloys into its jaw plates, increasing their lifespan and reducing maintenance needs. Sandvik employs cutting-edge heat treatment processes to enhance the strength and durability of its toggle plates. Terex incorporates modular designs into its components, simplifying installation and replacement.
These innovations not only improve the performance of jaw crusher parts but also reduce operational costs. Advanced technologies like self-lubricating bearings and anti-corrosion coatings further enhance the reliability of these components. By choosing parts from leading brands, you benefit from the latest advancements in the industry, ensuring your equipment operates at peak efficiency.
Comparison of Products
Side-by-side comparison of popular jaw crusher parts.
Comparing jaw crusher parts from different manufacturers helps you identify the best options for your needs. For instance, Metso’s jaw plates excel in wear resistance, making them ideal for abrasive materials. Sandvik’s toggle plates offer superior stability, ensuring consistent crushing performance. Terex’s pitman arms stand out for their robust construction, which minimizes stress on other components.
When evaluating products, consider factors like material quality, design features, and compatibility with your crusher model. High-manganese steel jaw plates from Metso provide exceptional toughness, while Sandvik’s alloy steel toggle plates balance strength and flexibility. Terex’s bearings feature advanced sealing systems that prevent contamination, extending their lifespan. A detailed comparison allows you to make informed decisions and select parts that deliver the best value.
Pros and cons of different brands and models.
Each manufacturer offers unique advantages, but no product is without limitations. Metso’s jaw plates provide excellent durability but may come at a higher cost. Sandvik’s toggle plates deliver reliable performance but require precise installation to function optimally. Terex’s modular components simplify maintenance but may not be compatible with all crusher models.
Understanding the pros and cons of each brand helps you weigh your options effectively. While Metso’s parts are ideal for demanding applications, Sandvik’s components suit operations requiring precision and stability. Terex’s products work well for users seeking ease of maintenance and versatility. By considering these factors, you can choose jaw crusher parts that align with your specific requirements and budget.
How to Choose the Right Jaw Crusher Parts for Your Application
Assessing Job Requirements
Factors to consider based on the type of material being crushed.
Understanding the material you need to crush is critical when selecting jaw crusher parts. Materials like granite, limestone, and recycled concrete have different levels of hardness and abrasiveness. Harder materials require parts made from tougher alloys, while softer materials may perform well with standard-grade components. Abrasive materials demand wear-resistant parts to minimize damage and extend their lifespan. By evaluating the material’s properties, you can choose parts that deliver optimal performance and durability.
Importance of matching parts to crusher specifications.
Every jaw crusher has unique specifications, including size, capacity, and operational requirements. Using parts that align with these specifications ensures efficient performance and prevents unnecessary strain on the machine. For example, oversized jaw plates may reduce crushing efficiency, while undersized toggle plates could compromise stability. Always consult your crusher’s manual or manufacturer to confirm compatibility. Matching parts to your crusher’s design enhances productivity and reduces the risk of mechanical failures.
Budget Considerations
Balancing cost with quality and performance.
Investing in jaw crusher parts requires balancing your budget with the need for quality and performance. Low-cost parts may seem appealing but often lead to frequent replacements and higher maintenance expenses. High-quality parts, though more expensive upfront, provide better durability and efficiency. Evaluate the long-term benefits of premium components to determine their value. Prioritizing quality over short-term savings ensures reliable operation and reduces overall costs.
Tips for finding cost-effective options without compromising durability.
You can find cost-effective jaw crusher parts by exploring reputable suppliers and comparing their offerings. Look for manufacturers that provide warranties or guarantees, as these indicate confidence in their products. Consider refurbished or aftermarket parts from trusted sources, which often deliver similar performance at a lower price. Bulk purchasing or establishing long-term supplier relationships may also help you secure discounts. By researching thoroughly, you can identify durable parts that fit your budget.
Compatibility and Customization
Ensuring parts are compatible with your specific crusher model.
Compatibility is essential when selecting jaw crusher parts. Using incompatible components can lead to operational inefficiencies and potential damage to your equipment. Verify part dimensions, material specifications, and design features to ensure they match your crusher model. Manufacturers often provide detailed compatibility charts or customer support to assist you. Confirming compatibility before purchase saves time and prevents costly errors.
Benefits of customized parts for unique applications.
Customized jaw crusher parts offer tailored solutions for specific operational needs. If your application involves unique materials or challenging conditions, custom parts can enhance performance and efficiency. For instance, specialized jaw plates designed for high-abrasion environments can improve wear resistance. Custom toggle plates may provide additional stability for heavy-duty tasks. Collaborating with manufacturers to create bespoke components ensures your crusher operates at its best, even in demanding scenarios.
Choosing the best jaw crusher parts ensures your equipment performs efficiently in heavy-duty applications. Durable materials, wear resistance, and precise compatibility play a crucial role in maintaining consistent results. Assess your job requirements carefully and research trusted brands to find components that meet your needs. Prioritize quality over short-term savings to reduce downtime and extend the lifespan of your crusher.
Investing in high-quality parts not only enhances performance but also minimizes long-term costs. Equip your crusher with reliable components to tackle tough jobs with confidence and achieve optimal productivity.
Post time: Nov-26-2024