Description
To produce top quality end products at the lowest cost with the highest efficiency and reliability, you have to select wear parts that are optimized for your particular crushing application. The main factors to consider as follow:
1. The type of rocks or minerals to be crushed.
2. Material particle size, moisture content and Mohs hardness grade.
3. The material and life of the blow bars previously used.
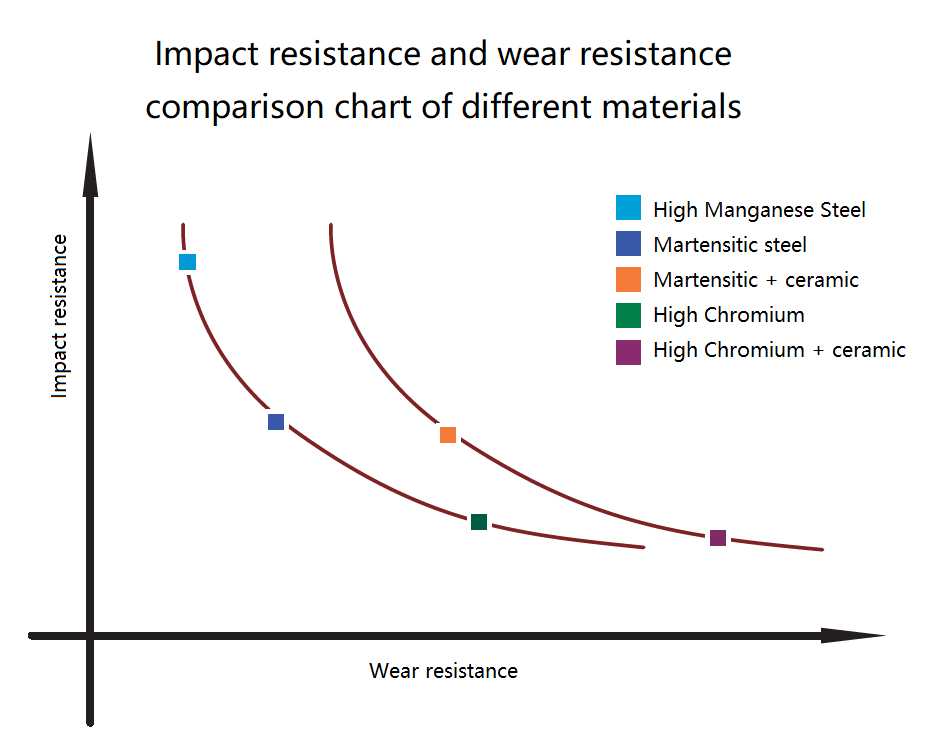
In general, the wear resistance (or hardness) of wall-mounted metal wear-resistant materials will inevitably reduce its impact resistance (or toughness). The method of embedding pottery in the metal matrix material can greatly increase its wear resistance without affecting its impact resistance.
High Manganese Steel
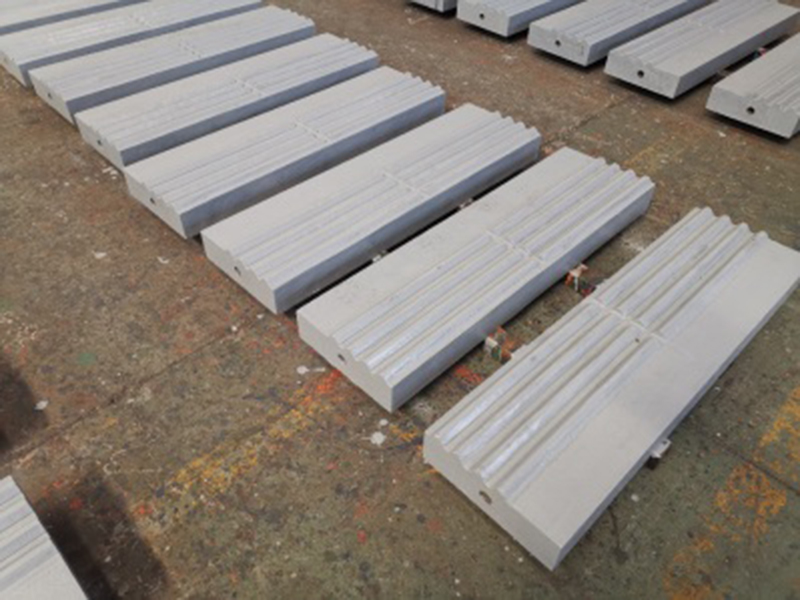
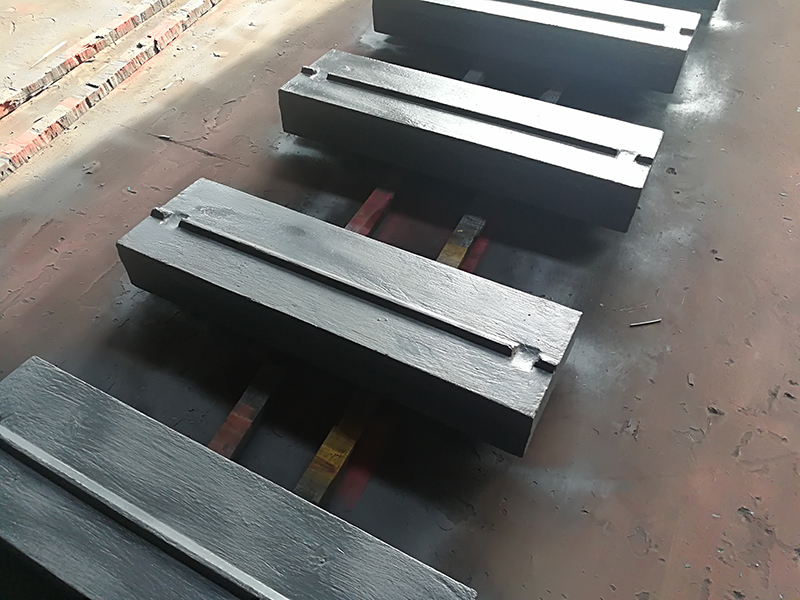
High manganese steel is a wear-resistant material with a long history and has been widely used in impact crushers. High manganese steel has outstanding impact resistance. The wear resistance is usually related to the pressure and impact on its surface. When a huge impact applied, the austenite structure on the surface can be hardened to HRC50 or higher.
High manganese steel plate hammers are generally only recommended for primary crushing with material of large feed particle size and low hardness.
Chemical composition of high manganese steel
Material |
Chemical Composition |
Machanical Property |
||||
Mn% |
Cr% |
C% |
Si% |
Ak/cm |
HB |
|
Mn14 |
12-14 |
1.7-2.2 |
1.15-1.25 |
0.3-0.6 |
> 140 |
180-220 |
Mn15 |
14-16 |
1.7-2.2 |
1.15-1.30 |
0.3-0.6 |
> 140 |
180-220 |
Mn18 |
16-19 |
1.8-2.5 |
1.15-1.30 |
0.3-0.8 |
> 140 |
190-240 |
Mn22 |
20-22 |
1.8-2.5 |
1.10-1.40 |
0.3-0.8 |
> 140 |
190-240 |
Microstructure of high manganese steel
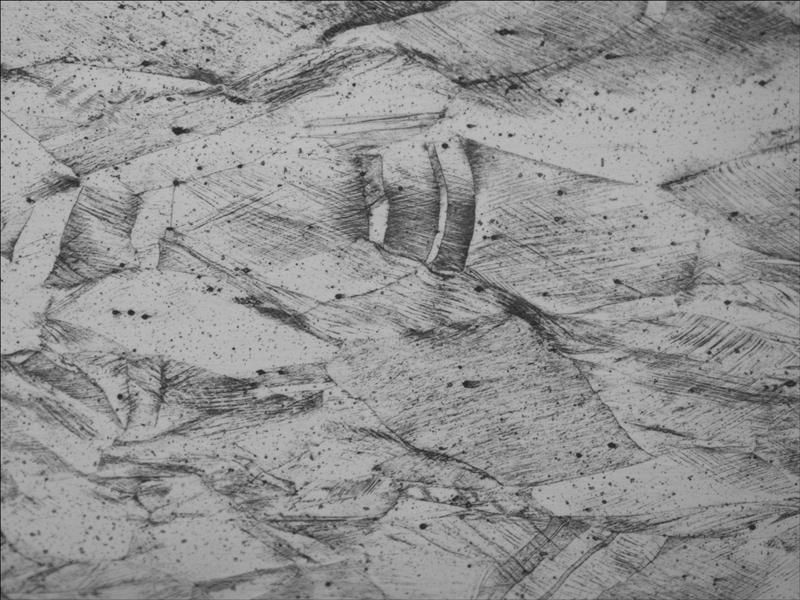
Martensitic Steel
Martensite structure is formed by rapid cooling of fully saturated carbon steel. The carbon atoms can diffuse out of martensite only in the rapid cooling process after heat treatment. Martensitic steel has a higher hardness than high-manganese steel, but its impact resistance is correspondingly reduced. The hardness of martensitic steel is between HRC46-56. Based on these properties, martensitic steel blow bar is generally recommended for crushing applications where relatively low impact but higher wear resistance is required.
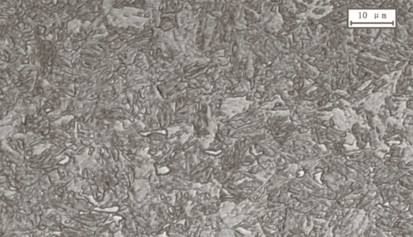
Microstructure of martensitic steel
High Chromium White Iron
In high chromium white iron, carbon is combined with chromium in the form of chromium carbide. High chromium white iron has outstanding wear resistance. After heat treatment, its hardness can reach 60-64HRC, but its impact resistance is correspondingly reduced. Compared with high manganese steel and martensitic steel, high chromium cast iron has the highest wear resistance, but its impact resistance is also the lowest.
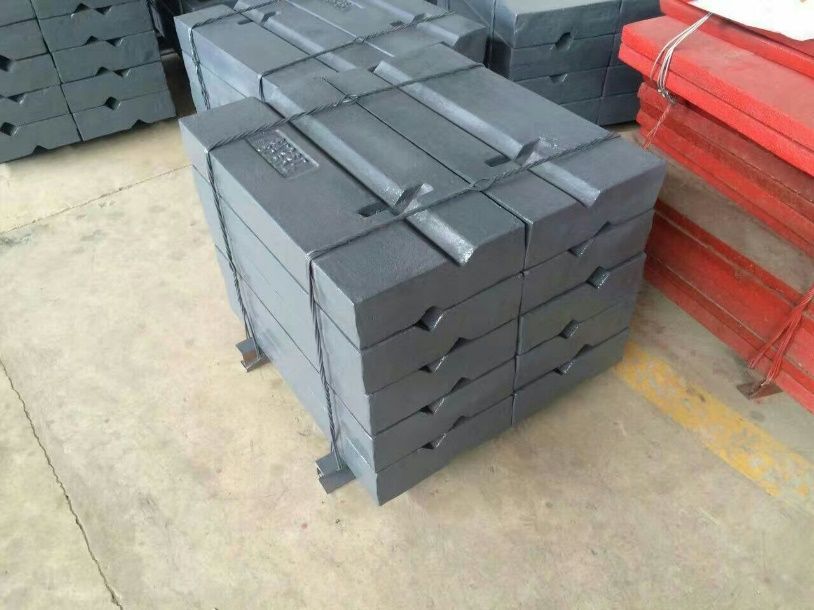
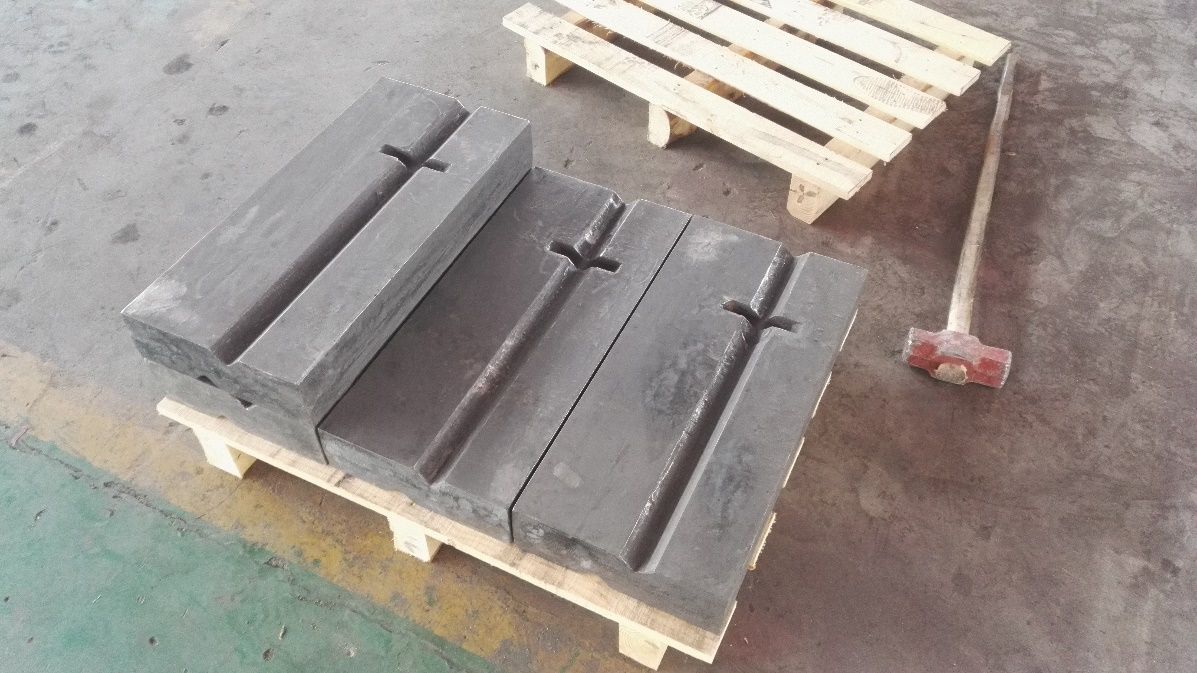
In high chromium white iron, carbon is combined with chromium in the form of chromium carbide. High chromium white iron has outstanding wear resistance. After heat treatment, its hardness can reach 60-64HRC, but its impact resistance is correspondingly reduced. Compared with high manganese steel and martensitic steel, high chromium cast iron has the highest wear resistance, but its impact resistance is also the lowest.
Chemical composition of high chromium white iron
ASTM A532 |
Description |
C |
Mn |
Si |
Ni |
Cr |
Mo |
|
I |
A |
Ni-Cr-Hc |
2.8-3.6 |
2.0 Max |
0.8 Max |
3.3-5.0 |
1.4-4.0 |
1.0 Max |
I |
B |
Ni-Cr-Lc |
2.4-3.0 |
2.0 Max |
0.8 Max |
3.3-5.0 |
1.4-4.0 |
1.0 Max |
I |
C |
Ni-Cr-GB |
2.5-3.7 |
2.0 Max |
0.8 Max |
4.0 Max |
1.0-2.5 |
1.0 Max |
I |
D |
Ni-HiCr |
2.5-3.6 |
2.0 Max |
2.0 Max |
4.5-7.0 |
7.0-11.0 |
1.5 Max |
II |
A |
12Cr |
2.0-3.3 |
2.0 Max |
1.5 Max |
0.40-0.60 |
11.0-14.0 |
3.0 Max |
II |
B |
15CrMo |
2.0-3.3 |
2.0 Max |
1.5 Max |
0.80-1.20 |
14.0-18.0 |
3.0 Max |
II |
D |
20CrMo |
2.8-3.3 |
2.0 Max |
1.0-2.2 |
0.80-1.20 |
18.0-23.0 |
3.0 Max |
III |
A |
25Cr |
2.8-3.3 |
2.0 Max |
1.5 Max |
0.40-0.60 |
23.0-30.0 |
3.0 Max |
Microstructure of High Chromium White Iron
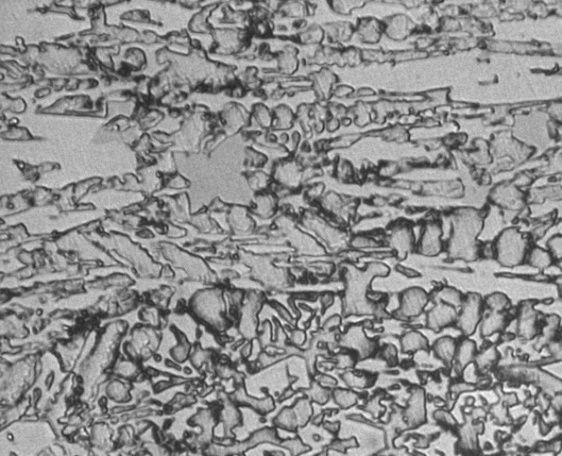
Ceramic-Metal Composite Material (CMC)
CMC is a wear-resistant material that combines the good toughness of metallic materials (martensitic steel or high-chromium cast iron) with the extremely high hardness of industry ceramics. Ceramic particles of a specific size are specially treated to form a porous body of ceramic particles. The molten metal penetrates completely into the interstices of the ceramic structure during casting and combines well with the pottery particles.
This design can effectively improve the anti-wear performance of the working face; at the same time, the main body of the blow bar or hammer is still made of metal to ensure its safe operation, effectively solving the contradiction between wear resistance and impact resistance, and can be adapted to a variety of working condition. It opens up a new field for the selection of high-wear spare parts for the majority of users, and create better economic benefits.
a.Martensitic Steel + Ceramic
Compared with the ordinary martensitic blow bar, the martensitic ceramic blow hammer has higher hardness on its wear surface, but the impact resistance of the blow hammer will not decrease. In the working conditions, the martensitic ceramic blow bar can be a good substitute for the application and usually can obtain nearly 2 times or longer service life.
b.High Chromium White Iron +Ceramic
Although ordinary high-chromium iron blow bar already has high wear resistance, when crushing materials with very high hardness, such as granite, more wear-resistant blow bars are usually used to prolong their working life. In this case, a high-chromium cast iron with inserted ceramic blow bar is a better solution. Due to the embedding of ceramics, the hardness of the wear surface of the blow hammer is further increased, and its wear resistance is significantly improved, usually 2 times or longer service life than normal high chromium white iron.
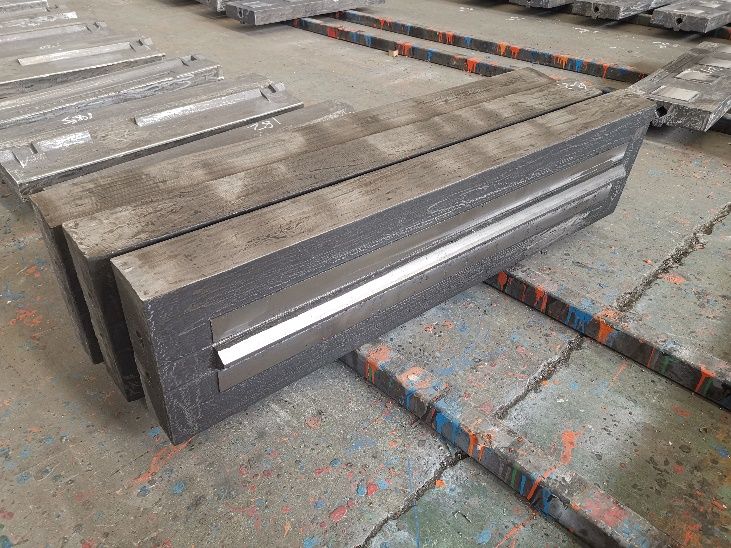
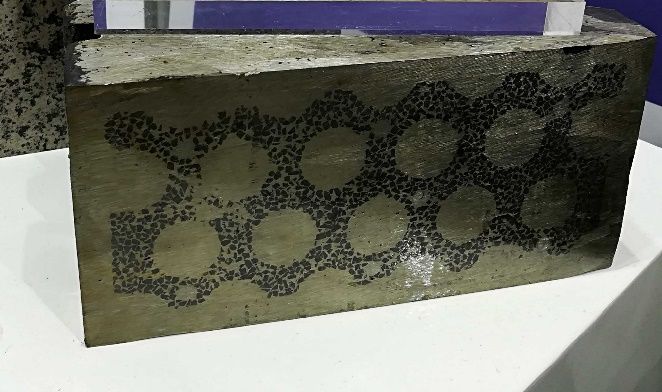
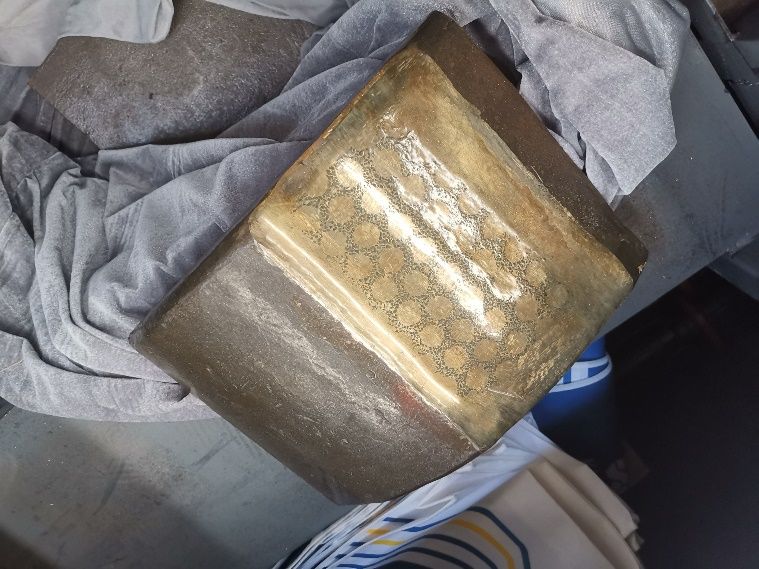
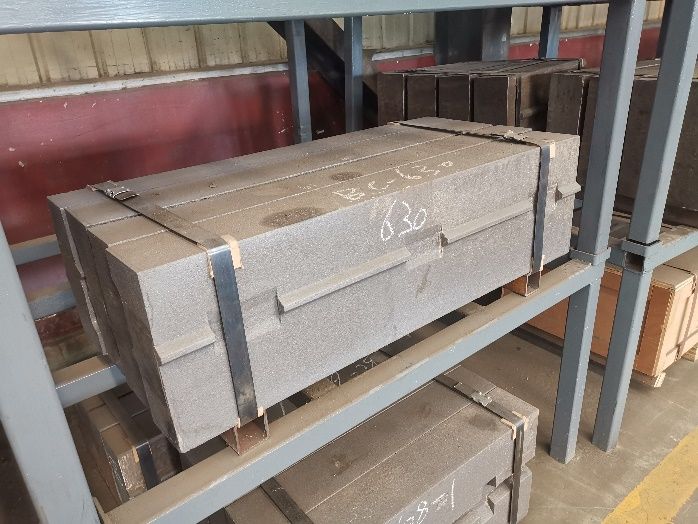
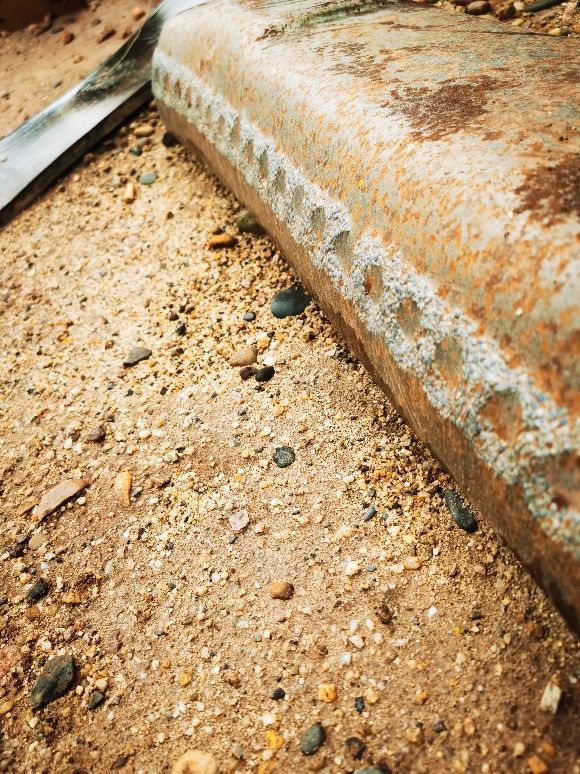
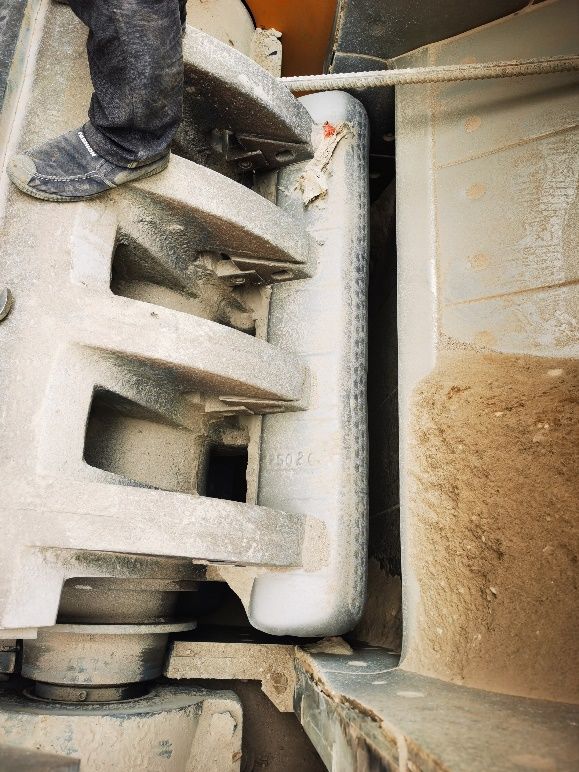
Advantages of Ceramic-Metal Composite Material (CMC)
(1) Hard but not brittle, tough and wear-resistant, achieving a dual balance of wear resistance and high toughness;
(2) The ceramic hardness is 2100HV, and the wear resistance can reach 3 to 4 times that of ordinary alloy materials;
(3) Personalized scheme design, more reasonable wear line;
(4) Long service life and high economic benefits.
Product Parameter
Machine Brand |
Machine model |
Metso |
LT-NP 1007 |
LT-NP 1110 | |
LT-NP 1213 | |
LT-NP 1315/1415 | |
LT-NP 1520/1620 | |
Hazemag |
1022 HAZ791-2 HAZ879 HAZ790 HAZ893 HAZ975 HAZ817 |
1313 HAZ796 HAZ857 HAZ832 HAZ879 HAZ764 HAZ1073 | |
1320 HAZ1025 HAZ804 HAZ789 HAZ878 HAZ800A HAZ1077 | |
1515 HAZ814 HAZ868 HAZ1085 HAZ866 HAZ850 HAZ804 | |
791 HAZ565 HAZ667 HAZ1023 HAZ811 HAZ793 HAZ1096 | |
789 HAZ815 HAZ814 HAZ764 HAZ810 HAZ797 HAZ1022 | |
Sandvik |
QI341 (QI240) |
QI441(QI440) | |
QI340 (I-C13) | |
CI124 | |
CI224 | |
Kleemann |
MR110 EVO |
MR130 EVO | |
MR100Z | |
MR122Z | |
Terex Pegson |
XH250 (CR004-012-001) |
XH320-new | |
XH320-old | |
1412 (XH500) | |
428 Tracpactor 4242 (300 high) | |
Powerscreen |
Trackpactor 320 |
Terex Finlay |
I-100 |
I-110 | |
I-120 | |
I-130 | |
I-140 | |
Rubblemaster |
RM60 |
RM70 | |
RM80 | |
RM100 | |
RM120 | |
Tesab |
RK-623 |
RK-1012 | |
Extec |
C13 |
Telsmith |
6060 |
Keestrack |
R3 |
R5 | |
McCloskey |
I44 |
I54 | |
Lippmann |
4248 |
Eagle |
1400 |
1200 | |
Striker |
907 |
1112/1312 -100mm | |
1112/1312 -120mm | |
1315 | |
Kumbee |
No1 |
No2 | |
Shanghai Shanbao |
PF-1010 |
PF-1210 | |
PF-1214 | |
PF-1315 | |
SBM/Henan Liming/Shanghai Zenith |
PF-1010 |
PF-1210 | |
PF-1214 | |
PF-1315 | |
PFW-1214 | |
PFW-1315 |