Video
Description
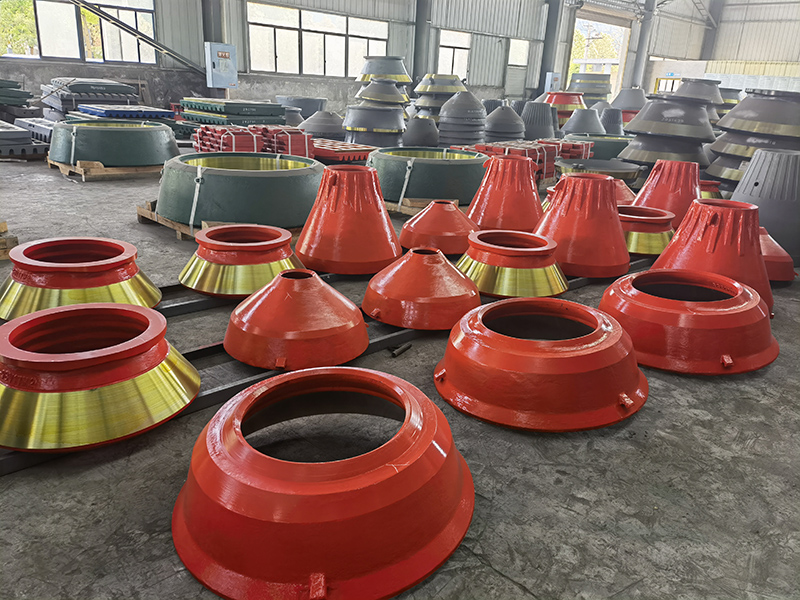
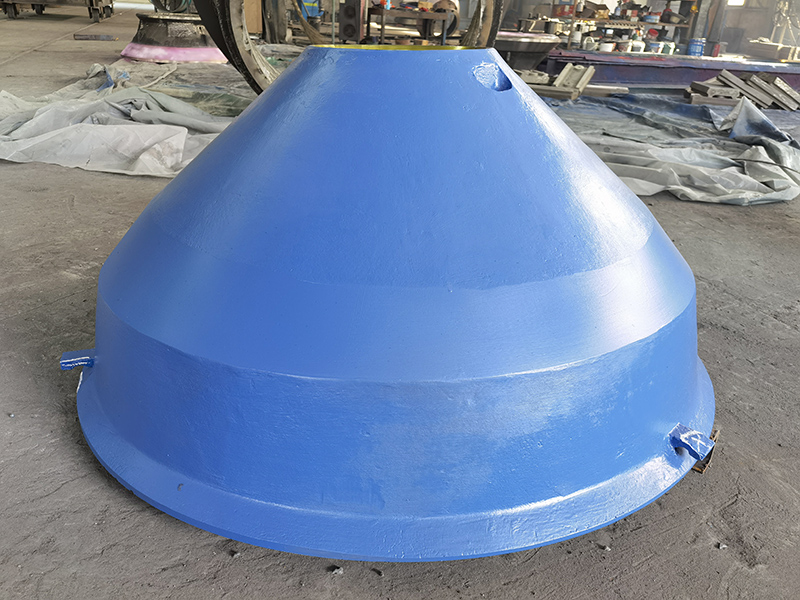
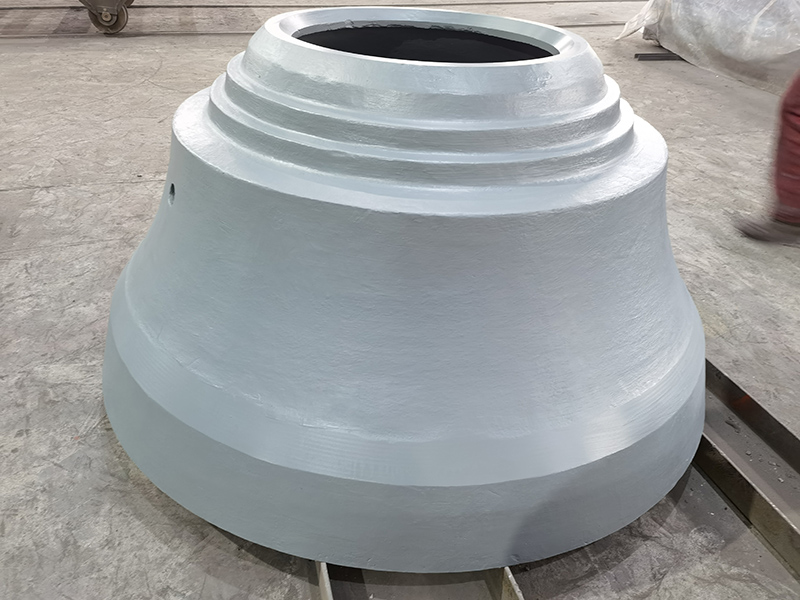
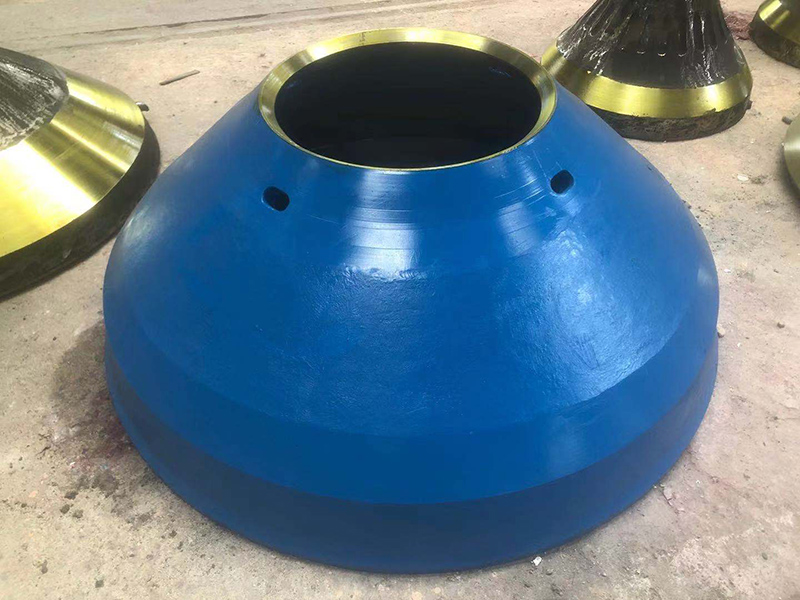
Sunrise has been deeply involved in manufacture the bowl liner and mantle. With suitable cavity design and material choose, our bowl liners and mantles and have been proven to perform better in the field, more so than the originals. Most of our cone liners are made of high manganese steel. It is widely used in rock crushing field. The quality and life time of bowl liner and mantle are determined by casting material and production process. All of Sunrise cone liner products are produced as per ISO9001:2008 quality system requests.
Product Parameter
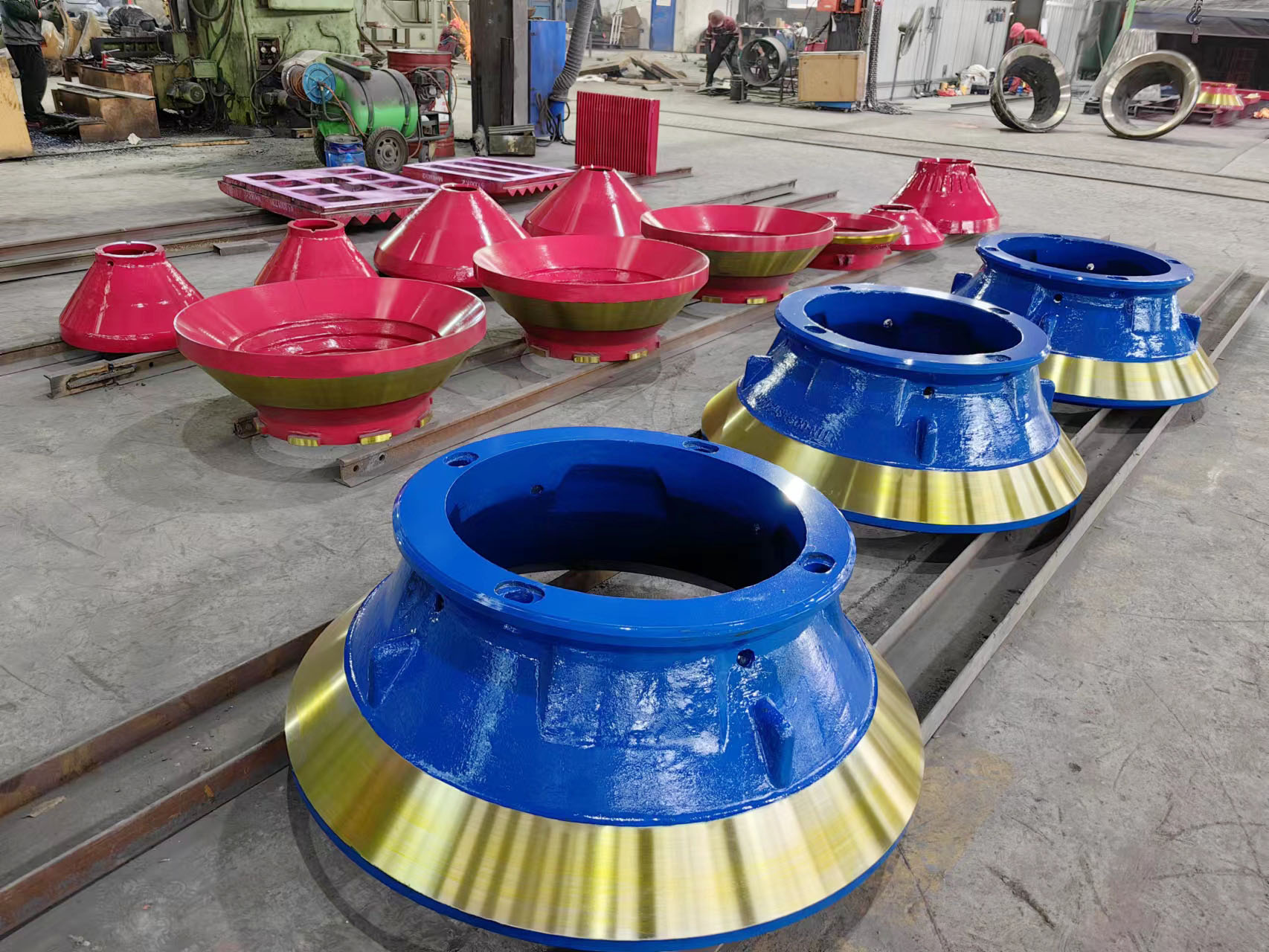
Chemical composition of Sunrise high manganese steel
Material |
Chemical Composition |
Machanical Property |
||||
Mn% |
Cr% |
C% |
Si% |
Ak/cm |
HB |
|
Mn14 |
12-14 |
1.7-2.2 |
1.15-1.25 |
0.3-0.6 |
> 140 |
180-220 |
Mn15 |
14-16 |
1.7-2.2 |
1.15-1.30 |
0.3-0.6 |
> 140 |
180-220 |
Mn18 |
16-19 |
1.8-2.5 |
1.15-1.30 |
0.3-0.8 |
> 140 |
190-240 |
Mn22 |
20-22 |
1.8-2.5 |
1.10-1.40 |
0.3-0.8 |
> 140 |
190-240 |
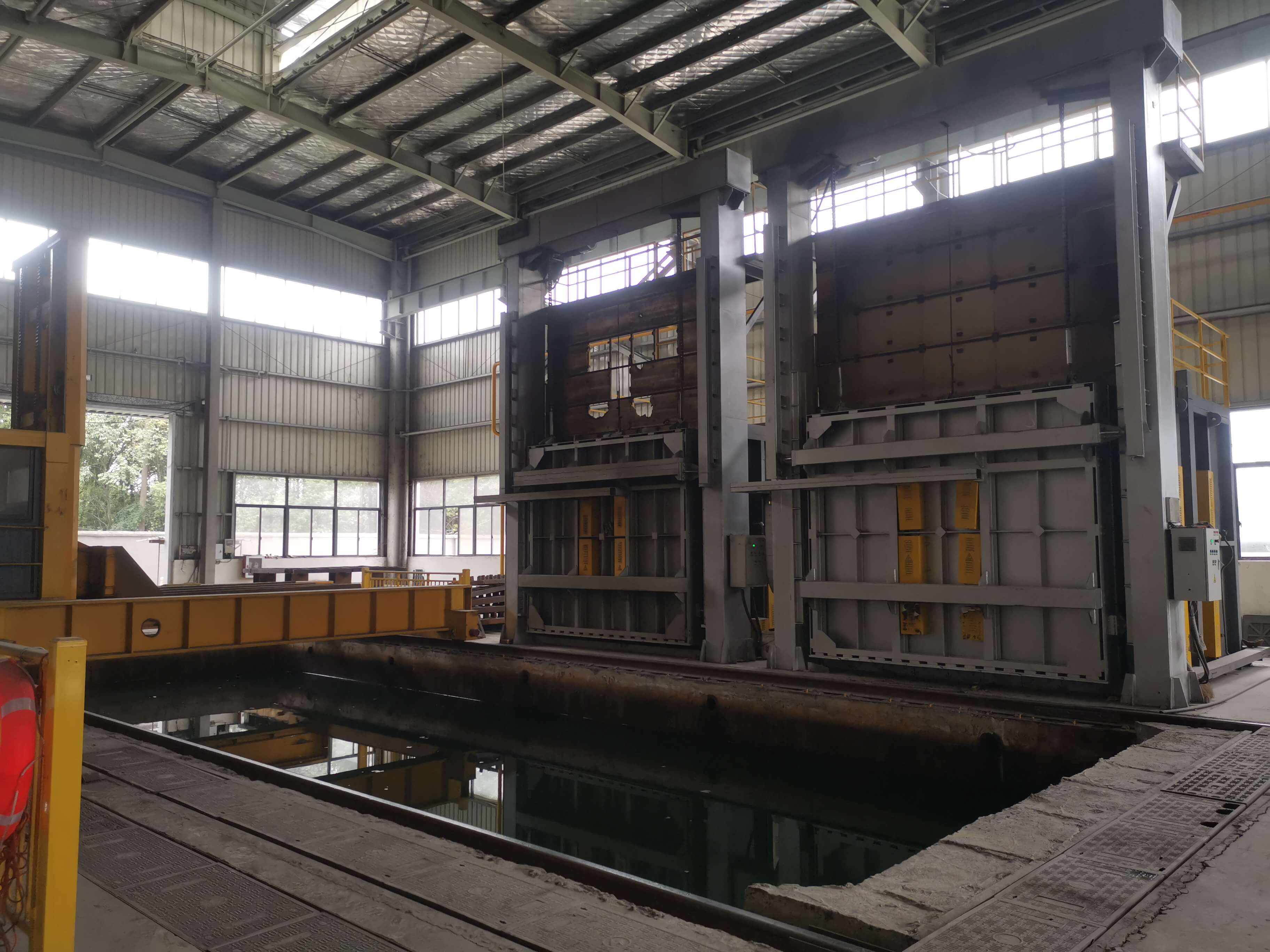
We use sodium silicate sand casting process. The raw material is excluding any recycling manganese steel which may contain other impurity. During the heat treatment process, we have automatic forklift to quench the parts after heat treatment woven in 35 seconds. It makes better metallographic structure and 20% longer lifetime than normal manganese.
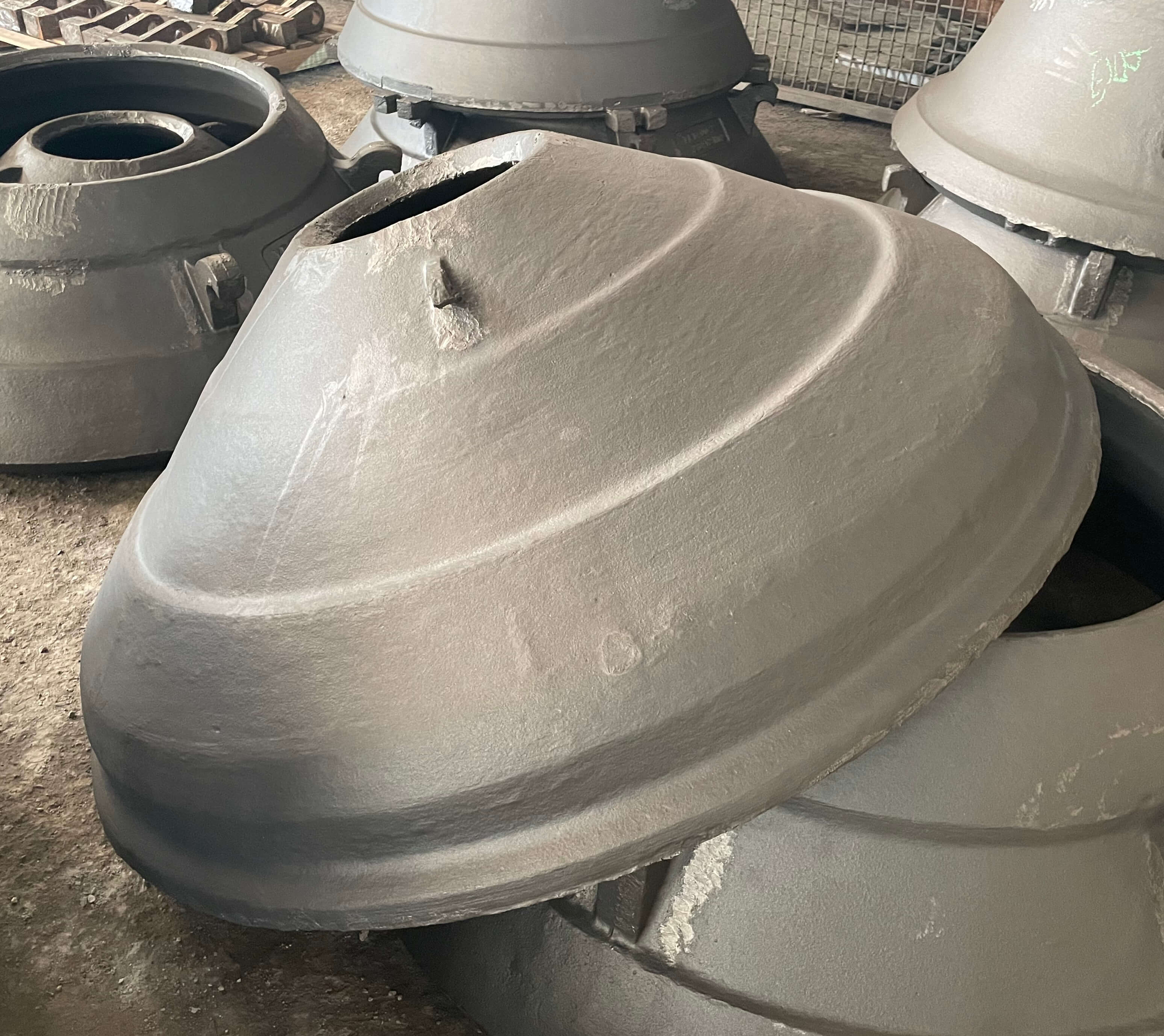
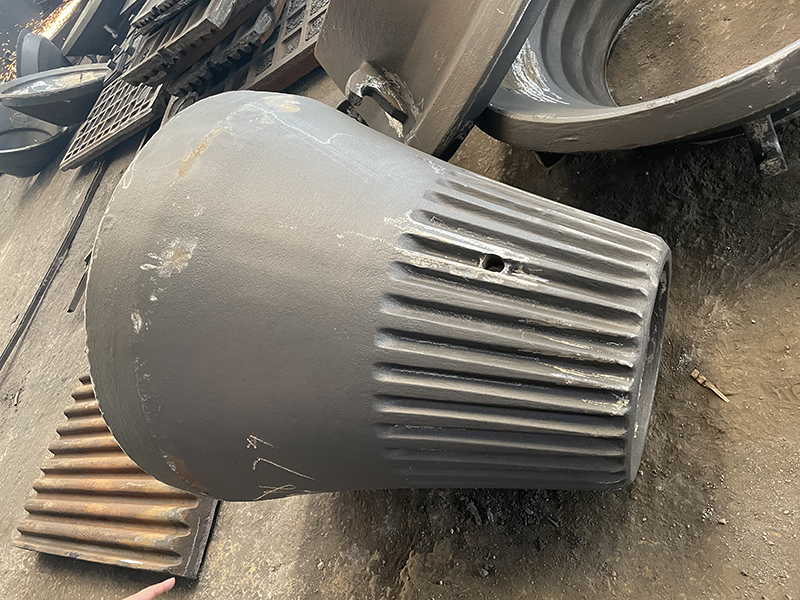
About This Item
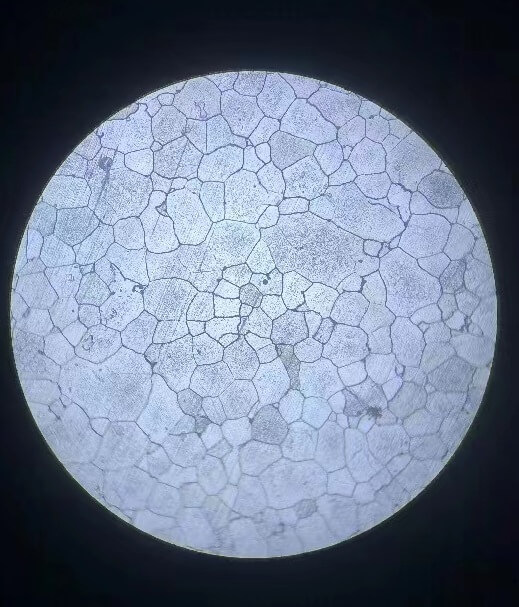
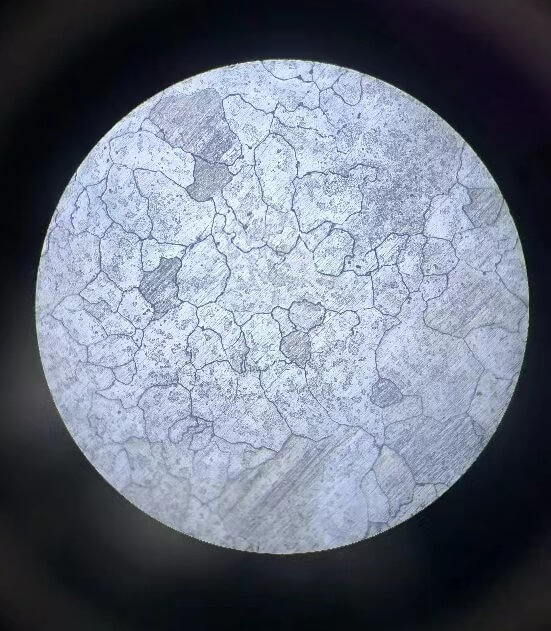
Our liner review and wear analysis focus on increasing life and production with custom-designed liners. For example,
A company based in Indonesia, were experiencing wear issues on their HP500 cone crusher. Processing approximately 550tph of very abrasive granite the standard Mn18 cone liners were lasting only a maximum of a week before requiring a change. This was reducing planned productivity and affecting the financial performance of the site. The solution that Sunrise offered is to use Heavy Duty Cone liners in material Mn18. It is based on the popular standard coarse chamber configuration and designed by our technical team. The newly designed concave and mantle Mn18 Heavy Duty cone liners were installed smoothly on the crusher. The wear life increased to 62hrs on the same application. This is an improvement of 45% over the standard liners which made a massive difference to the site productivity.
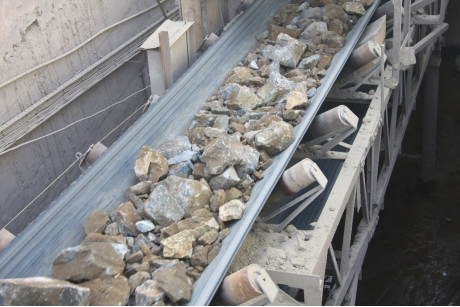
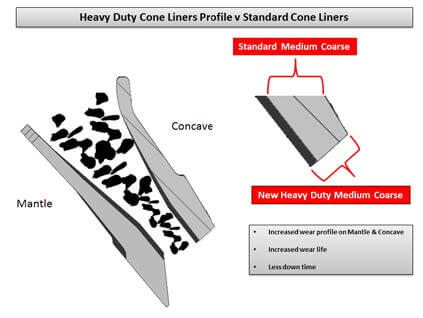