Key Takeaways
- The jaw crusher pitman is crucial for transferring motion and force, making it essential for the machine’s efficiency and safety.
- High-quality materials like cast steel and high manganese steel are vital for the pitman’s durability and performance under immense stress.
- Precision engineering and advanced manufacturing techniques, such as CAD and FEA, enhance the pitman’s design for optimal functionality.
- Heat treatment processes like quenching and tempering significantly improve the pitman’s strength and wear resistance, ensuring longevity.
- Rigorous quality control at every manufacturing stage guarantees that the pitman meets high standards for reliability and performance.
- A well-designed pitman not only boosts crushing power but also optimizes weight, contributing to the overall efficiency of jaw crushers.
Understanding the Jaw Crusher Pitman
The Jaw Crusher Pitman stands as a pivotal component in the operation of jaw crushers. Its design and functionality directly influence the machine’s performance, making it essential to understand its role and features. Let’s dive deeper into what makes this part so critical.
What Is a Jaw Crusher Pitman?
The pitman serves as the primary moving part of a jaw crusher. It connects the frame to the movable jaw and transfers the motion generated by the eccentric shaft. This motion enables the crushing mechanism to function effectively. Made from durable materials like cast steel or cast iron, the pitman withstands immense stress during operation. It moves in a reciprocating motion, much like the lower jaw chewing food, ensuring that materials are crushed efficiently as they pass through the chamber.
The pitman also features two key support points. The upper section connects to the flywheel and eccentric shaft, while the lower section interacts with the toggle plate, toggle seat, and tension rod. These connections ensure smooth movement and reliable performance under heavy loads.
Role of the Pitman in Jaw Crusher Operation
The pitman plays a central role in transferring force within the jaw crusher. As the eccentric shaft rotates, it drives the pitman to move up and down. This motion powers the crushing mechanism, enabling the machine to break down materials into smaller, usable sizes. Without the pitman, the jaw crusher would lack the necessary motion to perform its function.
Additionally, the pitman contributes to the machine’s safety and efficiency. Its robust construction ensures that it can handle the significant forces involved in crushing operations. By maintaining stability and precision, the pitman helps reduce energy consumption and enhances the overall productivity of the crusher.
Key Features of a High-Quality Pitman Component
A high-quality Jaw Crusher Pitman exhibits several essential features that ensure durability and performance:
- Material Strength: The pitman must be made from materials like cast steel or cast iron, which can endure high stress and resist wear over time.
- Precision Engineering: Accurate dimensions and tolerances are crucial for seamless integration with other components, such as the toggle plate and eccentric shaft.
- Lightweight Design with Enhanced Strength: Many pitmans incorporate a honeycomb structure in their lower section. This design reduces weight while increasing strength, improving operational efficiency.
- Reliable Support Points: The upper and lower support points must be robust to maintain stability during operation.
- Advanced Manufacturing Techniques: Techniques like computer-aided design (CAD) and finite element analysis (FEA) optimize the pitman’s design for maximum performance.
These features ensure that the pitman not only performs its function effectively but also contributes to the longevity and reliability of the jaw crusher.
Materials and Techniques in Manufacturing
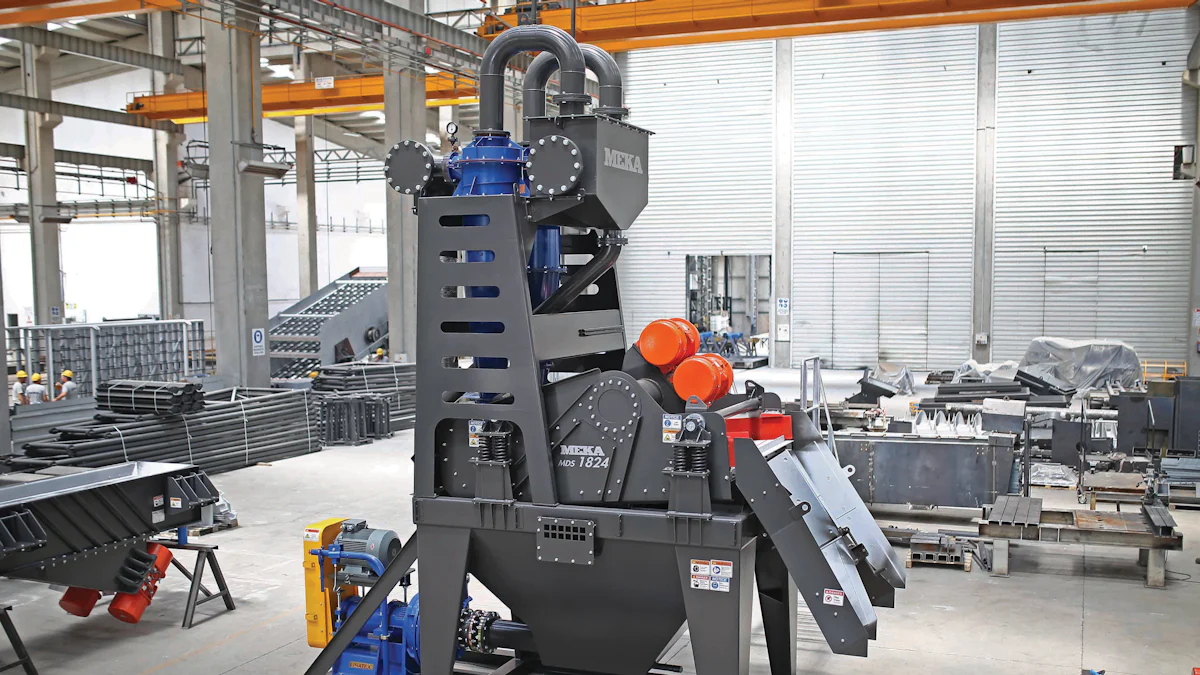
The manufacturing of a Jaw Crusher Pitman requires careful selection of materials and advanced techniques. These choices ensure the component can endure the immense forces it faces during operation while maintaining efficiency and durability.
Common Materials Used for Pitman Components
Manufacturers prioritize strength and durability when selecting materials for pitman components. The most commonly used materials include:
- Cast Steel: Known for its exceptional strength and resistance to wear, cast steel is a popular choice. It can handle the high stress and impact forces experienced during crushing operations.
- Wrought Iron: This material offers excellent toughness and malleability, making it suitable for components that require flexibility without compromising strength.
- High Manganese Steel: This material provides superior wear resistance, especially in applications involving heavy abrasion. Its self-hardening properties make it ideal for pitman components.
- Alloy Steel: With added elements like chromium or molybdenum, alloy steel enhances strength and resistance to corrosion, ensuring long-lasting performance.
Each material undergoes rigorous testing to meet industry standards. Manufacturers like Sunrise Machinery Co., Ltd ensure that only the highest-quality materials are used, guaranteeing reliability and longevity.
Importance of Material Selection for Durability and Performance
Material selection directly impacts the performance and lifespan of the pitman. A well-chosen material ensures the component can withstand the crushing forces without deforming or wearing out prematurely. For instance:
- Durability: High-strength materials like cast steel and high manganese steel resist wear and tear, reducing the need for frequent replacements.
- Performance: Lightweight materials with optimized strength, such as those with honeycomb structures, improve the crusher’s efficiency by reducing energy consumption.
- Safety: Robust materials prevent failures during operation, ensuring the safety of both the machinery and its operators.
At Sunrise Machinery Co., Ltd, we emphasize the importance of material quality. Our strict quality control process ensures every pitman meets the highest standards for durability and performance.
Overview of Casting and Forging Techniques
The manufacturing process for pitman components involves either casting or forging, each offering unique advantages:
-
Casting:
- Precision casting techniques allow manufacturers to create complex shapes with high accuracy.
- This method ensures uniformity in the component’s structure, enhancing its strength and reliability.
- Casting also enables the incorporation of design features like honeycomb structures, which reduce weight while maintaining strength.
-
Forging:
- Forging involves shaping the material under high pressure, resulting in a denser and stronger component.
- This technique improves the pitman’s ability to withstand bending and impact forces.
- Forged pitmans often exhibit superior mechanical properties, making them ideal for heavy-duty applications.
Both techniques require advanced tools and expertise. At Sunrise Machinery Co., Ltd, we utilize state-of-the-art equipment and skilled professionals to produce pitman components that meet the demands of modern jaw crushers.
Step-by-Step Manufacturing Process
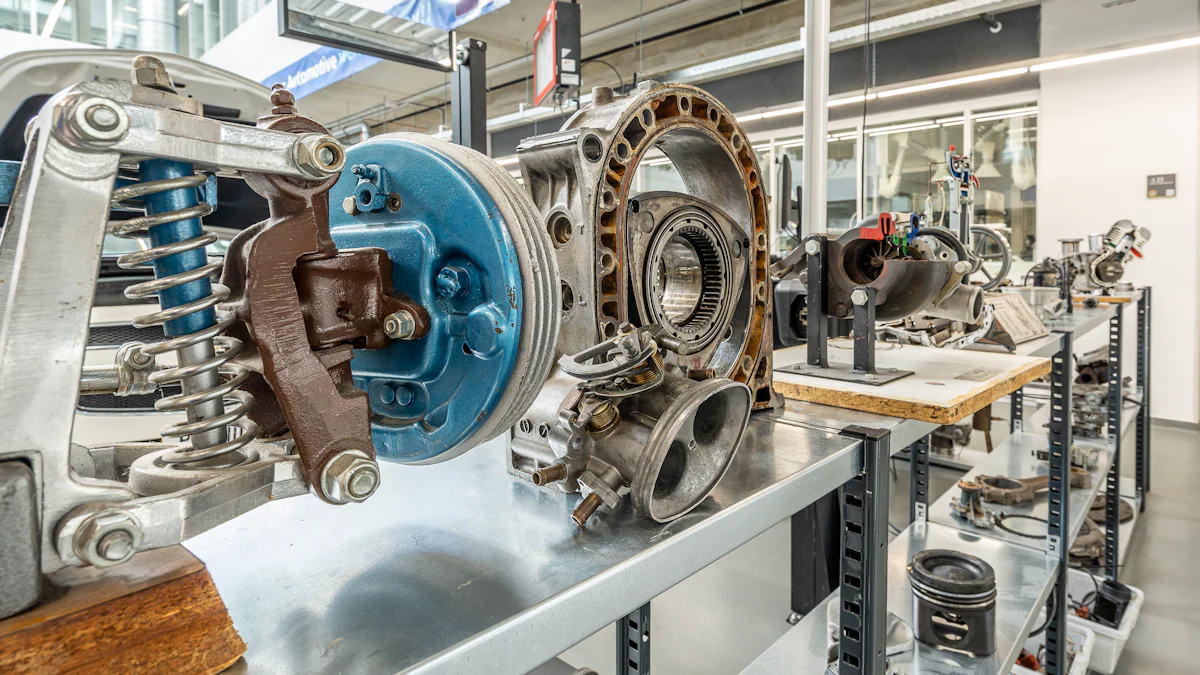
The manufacturing process of a Jaw Crusher Pitman involves several critical steps. Each step ensures the component meets the highest standards of durability, precision, and performance. Let’s explore the process in detail.
Material Selection and Preparation
Sourcing and Testing Raw Materials
The journey begins with sourcing high-quality raw materials. At Sunrise Machinery Co., Ltd, we prioritize materials like cast steel, cast iron, and high manganese steel. These materials are known for their strength and wear resistance. Before production, we test each batch of raw materials to ensure they meet strict quality standards. Tests focus on properties such as tensile strength, hardness, and chemical composition. This ensures the pitman can endure the immense forces it will face during operation.
Preparing Materials for Casting or Forging
Once the raw materials pass testing, we prepare them for the next stage. For casting, we melt the materials at precise temperatures to achieve a uniform composition. For forging, we heat the materials to make them malleable for shaping. Proper preparation minimizes defects and ensures the final product has consistent quality.
Casting or Forging the Pitman
Precision Casting Techniques
Casting is a popular method for creating pitman components. We use precision casting techniques to achieve complex shapes and detailed designs. This method allows us to incorporate features like honeycomb structures, which enhance strength while reducing weight. During casting, we carefully control the cooling process to prevent internal stresses and ensure structural integrity.
Forging Methods for Enhanced Strength
Forging involves shaping the heated material under high pressure. This method produces a denser and stronger pitman. Forged components exhibit superior mechanical properties, making them ideal for heavy-duty applications. At Sunrise Machinery Co., Ltd, we use advanced forging equipment to achieve precise dimensions and exceptional strength.
Machining and Shaping
Achieving Accurate Dimensions and Tolerances
After casting or forging, the pitman undergoes machining to achieve accurate dimensions. We use state-of-the-art CNC machines to ensure tight tolerances. This step is crucial for seamless integration with other jaw crusher components. Proper machining enhances the pitman’s performance and reliability.
Advanced Machining Tools and Techniques
We employ advanced tools and techniques to shape the pitman to perfection. Our skilled technicians use lathes, milling machines, and grinders to refine the component. This process ensures smooth surfaces and precise fits, which are essential for efficient operation. By focusing on every detail, we deliver pitman components that exceed industry standards.
Heat Treatment
Strengthening the Pitman Through Heat Treatment
Heat treatment plays a vital role in enhancing the strength and durability of the Jaw Crusher Pitman. By carefully controlling the heating and cooling processes, we can significantly improve the material’s mechanical properties. At Sunrise Machinery Co., Ltd, we focus on optimizing this step to ensure the pitman withstands the immense forces it encounters during operation.
The heat treatment process alters the internal structure of the material, making it tougher and more resistant to wear. For example, by applying specific temperatures and durations, we can increase the hardness of high manganese steel while maintaining its flexibility. This balance is crucial for components like the pitman, which must endure both compression and pulling forces without bending or breaking.
Our team uses advanced equipment to monitor every stage of the heat treatment process. This precision ensures consistent results, reducing the risk of defects and extending the lifespan of the pitman. By strengthening the material through heat treatment, we enhance the overall performance and reliability of the jaw crusher.
Common Heat Treatment Processes
We employ several heat treatment methods to achieve the desired properties in the pitman. Each process serves a specific purpose, ensuring the component meets the highest standards of quality and performance:
- Annealing: This process involves heating the material to a specific temperature and then cooling it slowly. Annealing reduces internal stresses, improves machinability, and enhances the material’s toughness.
- Quenching: By rapidly cooling the heated material, quenching increases hardness and wear resistance. This method is particularly effective for high manganese steel pitmans.
- Tempering: After quenching, tempering involves reheating the material to a lower temperature and then cooling it again. This step balances hardness and flexibility, preventing brittleness.
- Normalizing: This process refines the grain structure of the material, improving its strength and uniformity. Normalizing also enhances the pitman’s ability to withstand dynamic forces.
At Sunrise Machinery Co., Ltd, we tailor the heat treatment process to the specific requirements of each pitman. This customization ensures optimal performance and durability, even under the most demanding conditions.
Assembly and Finishing
Final Assembly of the Pitman Component
Once the heat treatment process is complete, we move on to the assembly stage. During this step, we integrate the pitman with other essential components of the jaw crusher. Precision is key here, as even minor misalignments can affect the machine’s performance.
Our skilled technicians use advanced tools to ensure a perfect fit between the pitman and parts like the toggle plate and eccentric shaft. We also conduct thorough inspections at this stage to verify that all connections are secure and meet our strict quality standards. By focusing on accuracy during assembly, we guarantee the smooth operation of the jaw crusher.
Surface Coating for Wear Resistance
The final step in the manufacturing process involves applying a surface coating to the pitman. This coating enhances the component’s resistance to wear and corrosion, further extending its lifespan. At Sunrise Machinery Co., Ltd, we use high-quality coatings that provide excellent protection without compromising the pitman’s performance.
For instance, we often apply specialized coatings designed to withstand the abrasive forces encountered during crushing operations. These coatings create a barrier that minimizes surface damage, reducing maintenance requirements and downtime. By investing in advanced surface treatments, we ensure the pitman remains reliable and efficient throughout its service life.
Quality Control in Pitman Manufacturing
Quality control plays a vital role in ensuring the reliability and performance of the Jaw Crusher Pitman. At Sunrise Machinery Co., Ltd, we follow a meticulous process to inspect and test every component at each stage of production. This guarantees that the pitman meets the highest standards of durability, precision, and safety.
Inspection and Testing at Each Stage
Dimensional Accuracy and Strength Testing
I believe that precision is the foundation of a high-quality pitman. During manufacturing, we measure every dimension with advanced tools to ensure accuracy. Even the smallest deviation can affect the pitman’s performance. By using cutting-edge equipment like coordinate measuring machines (CMM), we verify that the dimensions align perfectly with the design specifications.
Strength testing is equally important. The pitman must endure immense forces during operation. To confirm its durability, we conduct rigorous stress tests. These tests simulate real-world conditions, ensuring the pitman can handle heavy loads without deforming or failing. For example, we apply controlled pressure to evaluate its resistance to bending and impact forces. This step ensures that the pitman performs reliably under extreme conditions.
Ensuring Compliance with Industry Standards
Compliance with industry standards reflects our commitment to quality. At Sunrise Machinery Co., Ltd, we adhere to ISO-certified processes. These standards guide every aspect of production, from material selection to final inspection. By following these guidelines, we ensure that each pitman meets global benchmarks for safety and performance.
We also conduct chemical composition analysis to verify the material quality. This step ensures that the alloy content matches the required specifications. For instance, high manganese steel must have the right balance of elements to provide wear resistance and toughness. By maintaining strict compliance, we deliver pitman components that exceed customer expectations.
Final Quality Assurance Before Distribution
Before shipping, we perform a comprehensive quality check. This final inspection acts as a safeguard, ensuring that no defects go unnoticed. Our team examines every pitman for surface imperfections, structural integrity, and proper assembly. If any issue arises, we address it immediately to maintain our high standards.
Surface finishing receives special attention. A smooth and uniform coating enhances wear resistance and prevents corrosion. We use advanced techniques to apply protective layers, ensuring the pitman remains durable throughout its service life. This step not only improves performance but also reduces maintenance costs for our customers.
Finally, we package the pitman securely to prevent damage during transportation. Each component undergoes a final review to confirm it meets our strict quality criteria. By prioritizing quality assurance, we ensure that every pitman leaving our facility is ready to deliver exceptional performance.
The manufacturing process of the Jaw Crusher Pitman showcases the importance of precision and material quality at every stage. From selecting durable materials to employing advanced casting, forging, and heat treatment techniques, each step ensures the pitman can endure immense stresses while maintaining optimal performance. Rigorous quality control further guarantees reliability and longevity, reducing the risk of defects and enhancing operational efficiency. A well-designed pitman not only improves crushing power but also optimizes weight and durability, contributing to the overall success of jaw crushers in demanding applications.
FAQ
What is a Pitman in a Jaw Crusher?
The pitman serves as the main moving part of a jaw crusher. It connects the eccentric shaft to the crushing mechanism, transferring motion and force to crush materials effectively. This component plays a vital role in ensuring the efficiency and safety of the crusher. Without the pitman, the jaw crusher cannot function properly.
What is the role of the Pitman in a Jaw Crusher?
The pitman transfers the force generated by the toggle plate to the crushing mechanism. It moves up and down as the eccentric shaft rotates, enabling the crushing process. The pitman also ensures stability and precision during operation. Its robust construction allows it to handle immense stress and strain, making it a key component in the crusher’s performance.
How is the Pitman Manufactured?
Manufacturing the pitman involves several steps, including material selection, casting or forging, machining, heat treatment, and assembly. High-quality materials like cast steel or high manganese steel are used to ensure durability. Advanced techniques such as precision casting and forging enhance strength and reliability. Heat treatment further improves the pitman’s mechanical properties, ensuring it can withstand heavy loads.
What Materials Are Used to Make the Pitman?
Manufacturers use materials like cast steel, high manganese steel, wrought iron, and alloy steel to produce the pitman. These materials offer excellent strength, wear resistance, and durability. The choice of material depends on the specific requirements of the jaw crusher and the operating conditions.
How Can the Quality of the Pitman Be Improved?
Improving the pitman’s quality involves optimizing the manufacturing process. Reducing work phases, speeding up production, and using less material can enhance efficiency. Machining the edges of the webs and optimizing the weight of the pitman improve its performance. Regular inspections and testing ensure the final product meets high-quality standards.
Why Is Material Selection Important for the Pitman?
Material selection directly impacts the pitman’s durability and performance. High-strength materials resist wear and tear, reducing the need for frequent replacements. Lightweight materials with optimized strength improve the crusher’s efficiency. Robust materials also ensure safety by preventing failures during operation.
What is the Main Moving Part in a Jaw Crusher?
The pitman is the main moving part in a jaw crusher. It forms the moving side of the jaw and drives the crushing mechanism. Its movement enables the crusher to break down materials into smaller sizes.
How Does Heat Treatment Enhance the Pitman?
Heat treatment strengthens the pitman by altering its internal structure. Processes like annealing, quenching, and tempering improve hardness, toughness, and wear resistance. These treatments ensure the pitman can endure the immense forces it faces during operation.
What Makes a High-Quality Pitman?
A high-quality pitman features strong materials, precise dimensions, and advanced design elements like honeycomb structures. It undergoes rigorous testing to ensure durability and performance. Reliable support points and surface coatings further enhance its efficiency and lifespan.
Why Choose Sunrise Machinery Co., Ltd for Pitman Components?
At Sunrise Machinery Co., Ltd, we prioritize quality and precision. With over 20 years of experience, we use advanced techniques and high-quality materials to manufacture pitman components. Our strict quality control process ensures every product meets international standards. We also offer customized services to meet specific customer needs, making us a trusted choice worldwide.
Post time: Dec-30-2024